At FarmSkins, transparency is one of our core values. That's why we're pulling back the curtain to give you an inside look at our manufacturing process. From carefully selecting raw materials to delivering the finished product, we've developed a production system that minimizes environmental impact while maximizing quality and performance.
Step 1: Sourcing Sustainable Raw Materials
Our commitment to sustainability begins with sourcing. We use three primary categories of raw materials:
- Agricultural Byproducts: We partner with local farms to repurpose materials that would otherwise be discarded—wheat straw, rice husks, corn stalks, and sugarcane bagasse. This creates additional revenue streams for farmers while diverting waste from landfills.
- Sustainably Harvested Seaweed: For our flexible films and coatings, we use seaweed harvested using methods that allow for rapid regeneration. Our harvesting practices follow strict ecological guidelines to maintain marine ecosystem health.
- Fungal Cultures: Our mushroom-based packaging starts with carefully selected fungal strains grown in controlled environments on agricultural waste substrates.
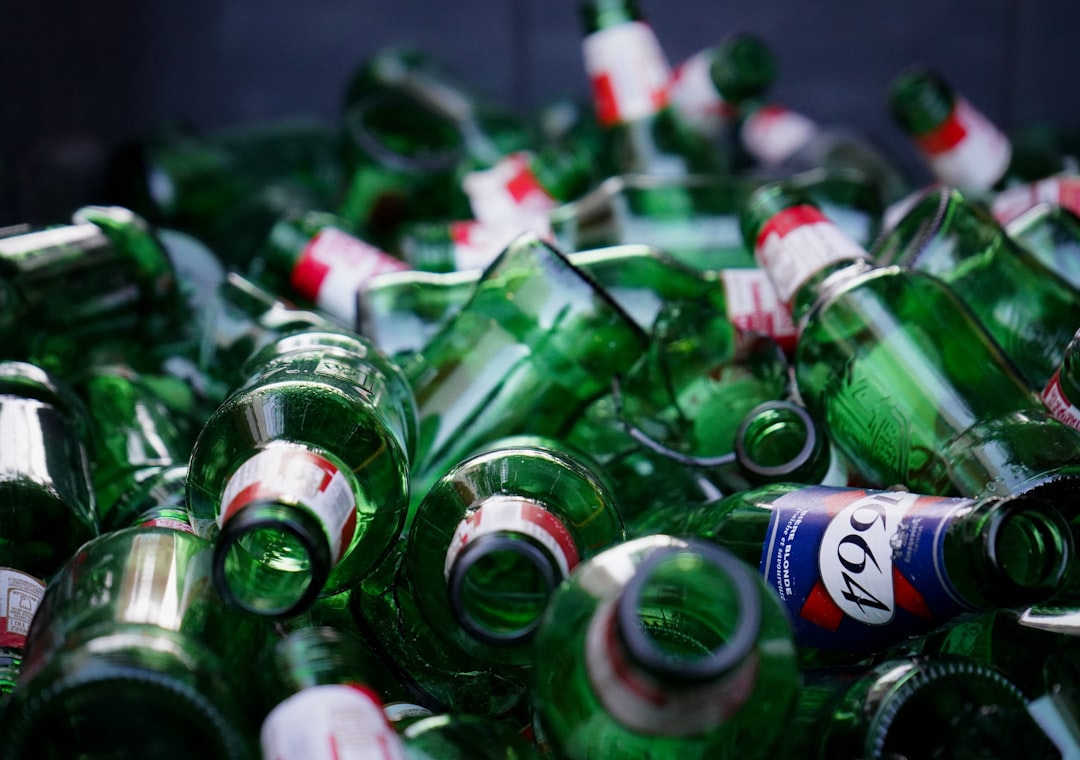
Our team inspecting locally sourced agricultural byproducts before processing
Step 2: Material Preparation and Processing
Once materials arrive at our facility, they undergo careful preparation:
For Agricultural Fiber-Based Products:
- Cleaning: Raw materials are cleaned to remove any contaminants.
- Mechanical Processing: Using low-energy mechanical methods, we break down fibers to the optimal size and consistency.
- Natural Binding: Rather than synthetic adhesives, we use plant-based binders derived from starches and proteins to create cohesive materials.
- Additive Integration: When necessary, we incorporate natural additives for water resistance, UV protection, or antimicrobial properties.
For Seaweed-Based Films:
- Extraction: Using water-based processes, we extract the natural polymers from seaweed.
- Filtration: The extract undergoes multiple filtration stages to ensure purity.
- Formulation: We blend the extract with other natural ingredients to achieve specific performance characteristics.
- Film Formation: The solution is cast into films using our proprietary spreading technology that minimizes energy use.
For Mycelium-Based Products:
- Substrate Preparation: Agricultural waste is pasteurized using steam rather than chemicals.
- Inoculation: Fungal cultures are introduced to the substrate.
- Growth Period: The mycelium grows through the substrate in temperature and humidity-controlled environments.
- Deactivation: Once the desired density is achieved, the living material is deactivated using heat.
"Our manufacturing philosophy is simple: work with nature's processes rather than against them. This approach not only yields superior materials but does so with a fraction of the environmental impact of conventional methods." — Robert Chen, CTO of FarmSkins
Step 3: Molding and Forming
The prepared materials are then shaped into final products using various techniques:
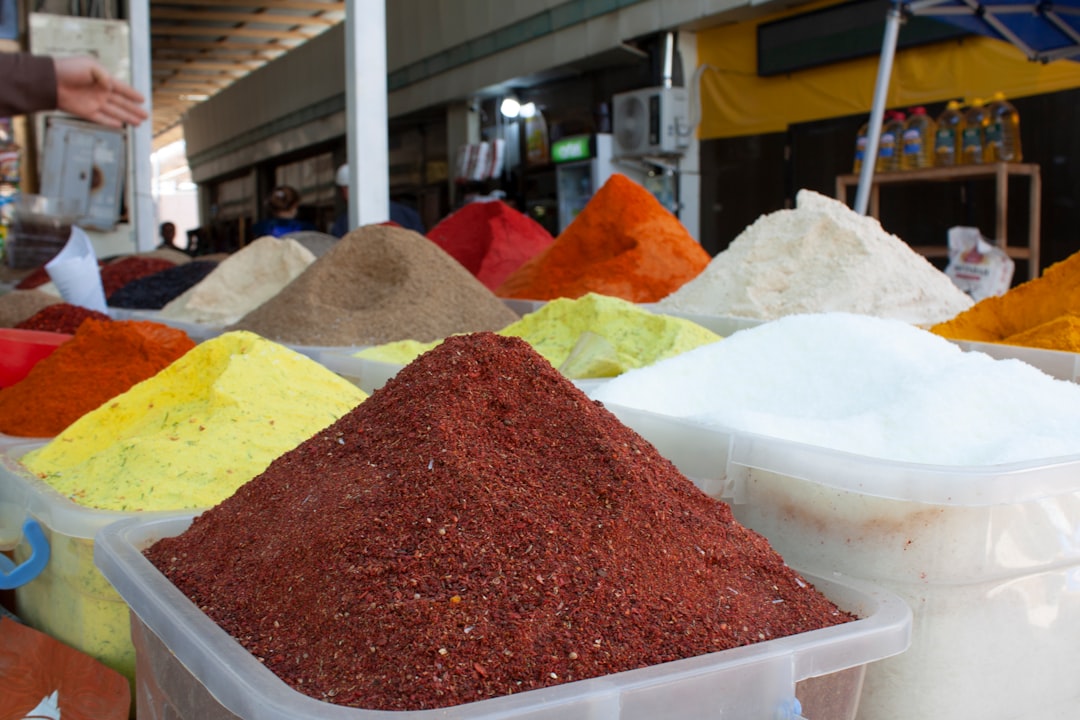
Our compression molding process for agricultural fiber containers
- Compression Molding: For fiber-based products, we use low-pressure compression molding that requires 70% less energy than traditional plastic molding processes.
- Casting: Our films are cast on energy-efficient conveyor systems that recapture and reuse water from the process.
- Grown-in-Place: Mycelium products are grown directly in reusable molds, taking on the exact shape needed without additional forming steps.
Our forming processes use electric systems powered by renewable energy. Our UK manufacturing facility operates on 100% renewable electricity, while our international facilities maintain a minimum of 70% renewable energy use.
Step 4: Finishing and Quality Control
Each product undergoes finishing and rigorous quality testing:
Finishing Processes:
- Trimming: Excess material is removed and returned to the production cycle.
- Surface Treatment: When needed, natural water-resistant or barrier coatings are applied.
- Drying: Products are dried using energy-efficient heat recovery systems.
Quality Control:
Every batch undergoes a comprehensive testing regimen to ensure it meets our standards:
- Physical Properties: Strength, flexibility, and durability are tested to meet or exceed industry standards.
- Barrier Performance: We measure oxygen, moisture, and light barrier properties for packaging that requires protection.
- Biodegradability: Samples from each batch are subjected to composting tests to verify decomposition rates.
- Food Safety: For food-contact materials, we conduct migration tests to ensure no harmful substances transfer to food.
Step 5: Waste Management and Circular Systems
We've designed our production system to minimize waste at every stage:
- Production trimmings and rejects are reincorporated into new batches when possible.
- Water used in production is filtered and reused in closed-loop systems.
- Any organic waste that cannot be reused in production becomes compost that fertilizes our test gardens, where we grow some of our own raw materials.
This circular approach has allowed us to achieve a remarkable 98.5% waste diversion rate across all our facilities.
Step 6: Packaging and Distribution
Our sustainability commitment extends to how we package and ship our products:
- Products are packed using our own organic packaging materials.
- We optimize shipping densities to reduce transportation emissions.
- Our logistics partners are selected based on their sustainability commitments and carbon reduction strategies.
- We offset all unavoidable shipping emissions through verified carbon offset projects.
Continuous Improvement through Innovation
Our manufacturing process is never static. We maintain a dedicated research and development team that continually works to:
- Reduce energy and water consumption in production
- Develop new bio-based materials with enhanced properties
- Improve efficiency to make sustainable packaging more affordable
- Create new applications for organic packaging technology
Recent innovations include a 30% reduction in drying energy requirements and a new rapid-composting formula that accelerates biodegradation by 40% in home composting environments.
Certifications and Standards
Our manufacturing processes are certified to meet or exceed numerous international standards:
- ISO 14001 Environmental Management System
- ISO 9001 Quality Management System
- EU Organic Production certification
- Biodegradable Products Institute (BPI) certification
- Carbon Trust Standard
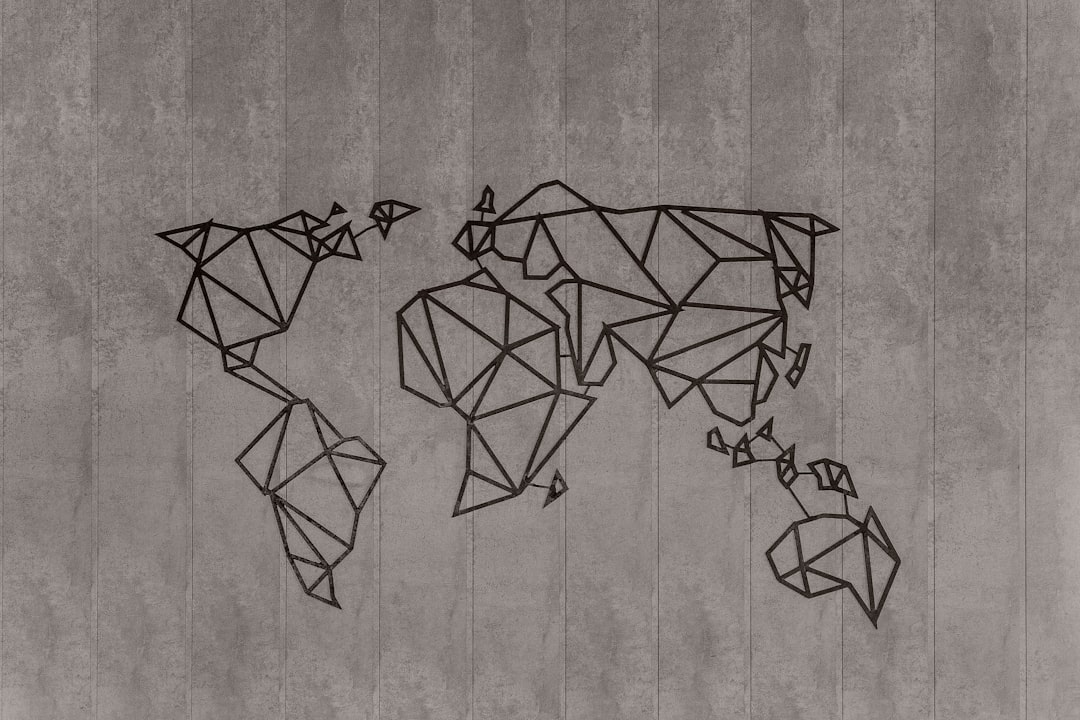
Our lab technicians conducting quality and performance tests
Visit Our Facilities
We believe in transparency and offer scheduled tours of our manufacturing facilities to customers, partners, and educational groups. These tours provide an opportunity to see firsthand how we transform natural materials into high-performance packaging.
If you're interested in visiting, please contact us through our website to schedule a tour at one of our locations.
Conclusion
Our manufacturing process represents our commitment to proving that sustainable production can be both environmentally responsible and economically viable. By working with natural materials and processes, we're creating packaging solutions that protect products without compromising our planet's future.
As we continue to grow and evolve, our manufacturing principles remain constant: respect for natural resources, commitment to quality, and innovation that drives positive environmental impact.